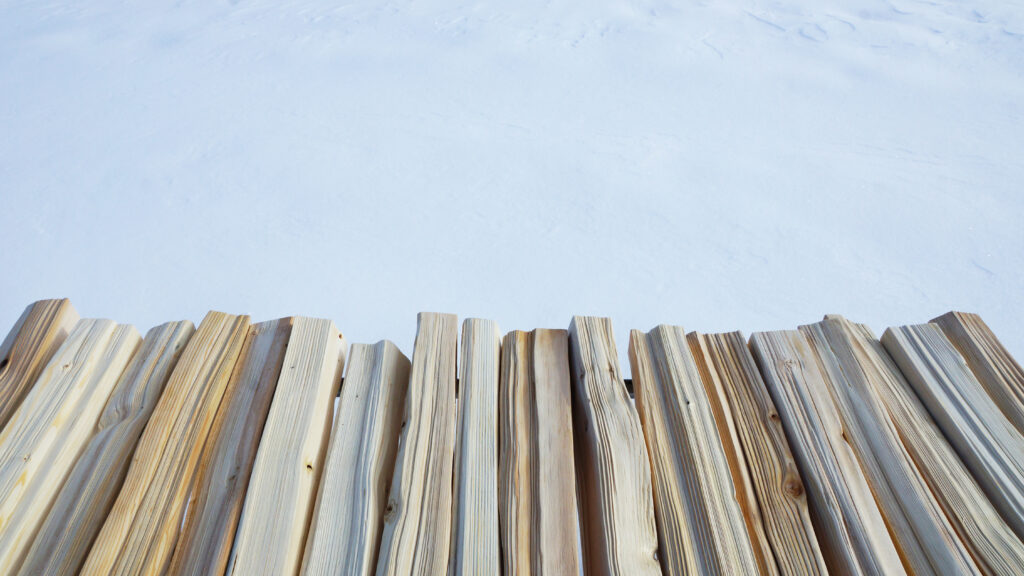
NATURAL SURFACE
IN CONVERSATION WITH
DR. MARTIN SCHNEEBELI
FB: Observing snow, one can’t help but notice the dynamic changes its surface undergoes. Could you explain what factors predominantly affect these alterations in the snow’s top layer?
MS: The transformation of the snow’s surface is primarily influenced by several environmental factors. Wind plays a significant role; it can transport loose snow, fragmenting the crystals and redepositing them elsewhere. Solar radiation is another crucial factor—the snow absorbs sunlight, which can lead to warming, compaction, and even melting of the surface layer. Additionally, long-wave radiation, particularly in the far-infrared spectrum, significantly impacts snow. Snow acts as a black body for these wavelengths, resulting in rapid cooling of the surface layer. This cooling can make the surface cooler than the surrounding air, leading to the formation of surface frost. Such conditions are critical for the development of avalanches, highlighting the complex interplay of environmental factors on the snow’s surface dynamics.
OMAMAME
2022
The table serves as a creative testament to the dynamic and ever-changing surface of snow, aiming to shine a light on the intricate qualities of snow cover. Just as every centimeter of wood grain tells a unique story, so does each segment of the snow’s surface. This piece of furniture invites observers to appreciate the fine details and the natural beauty present in both the wood it is crafted from and the snow it represents. By drawing this parallel, the table not only functions as a practical item but also as a medium for reflection on the diversity and richness of nature’s designs, encouraging a closer look at the world around us and the unique patterns that define it.
Materials: 18x firewood of different length, spruce, larch, beech- 8x iron pipe of different length Ø20mm – Dimension: 1450mm X 700mm X 760mm
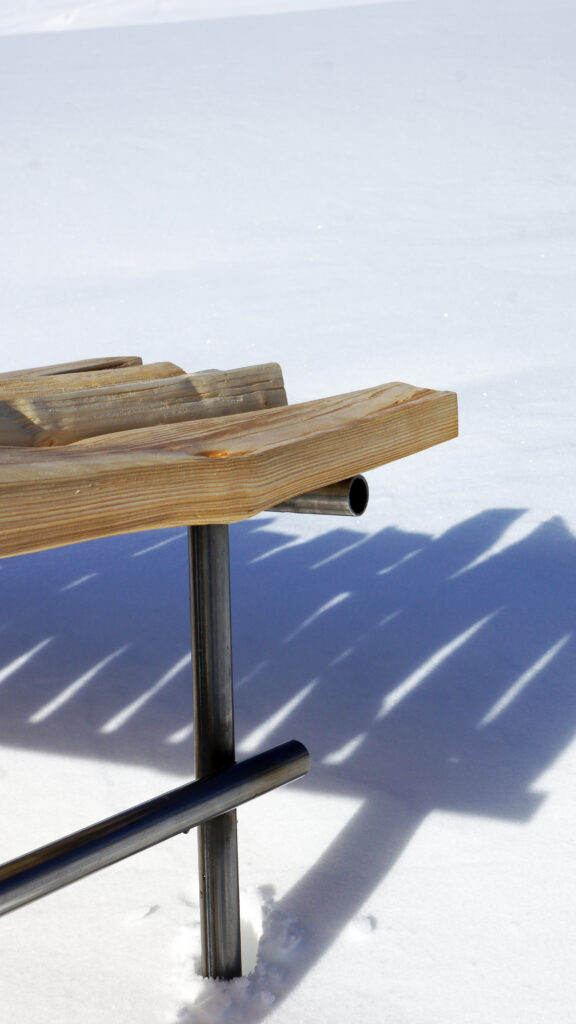
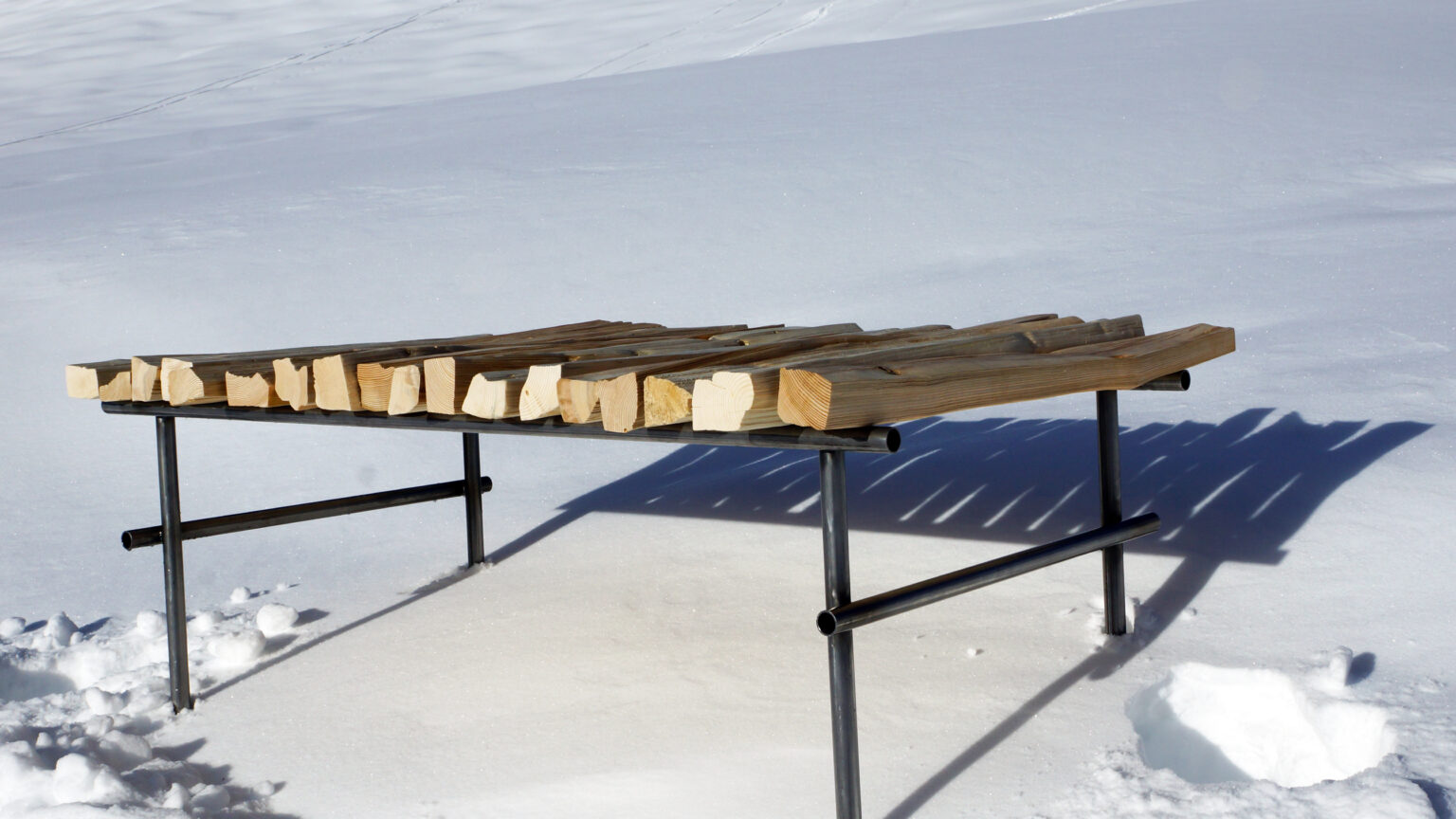
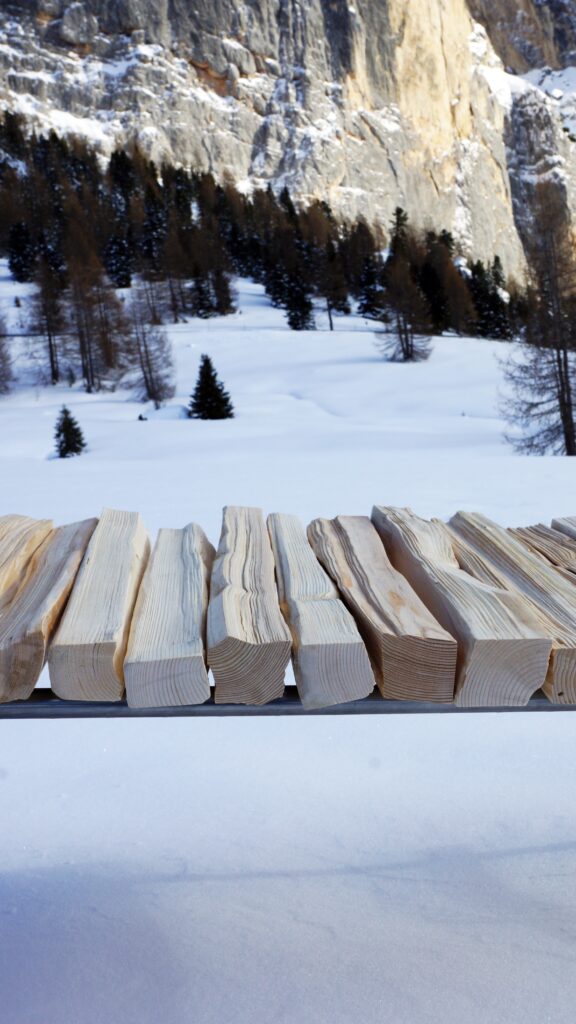
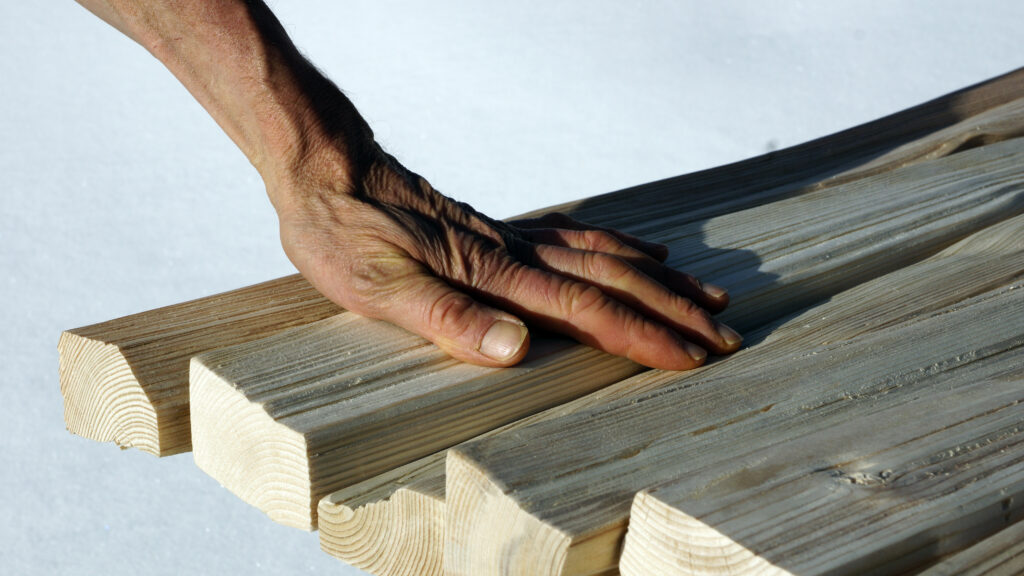
PROCESS
COLLABORATION:
GALEVI
Firewood has something very special about it. Since childhood, once a day in the winter the stove is turned on and immediately spreads a serene mood. However, too little attention is paid to the aesthetics of this processed type of wood. It illustrates the interaction between man and nature very well. The tree grows, is felled, crushed and split. When it is split, however, it is man on the one hand, and wood on the other, that decide where it is separated. The fibers of the wood influence the splitting and a form is created between natural shaping and human intervention.
The curls and cavities in the wood are reminiscent of the surface of snow. Each piece is unique, just as each square inch of the snow surface is unique. This visual layer is completed by a haptic one. Unfortunately, you can not experience the haptic qualities of the wood peaks because it is very easy to get a slate; I felt that many times during processing. The violence which these individual woods are made with, reflect the power of the snow. The wood, which is basically used to donate heat, contrasts with the cold material of snow.
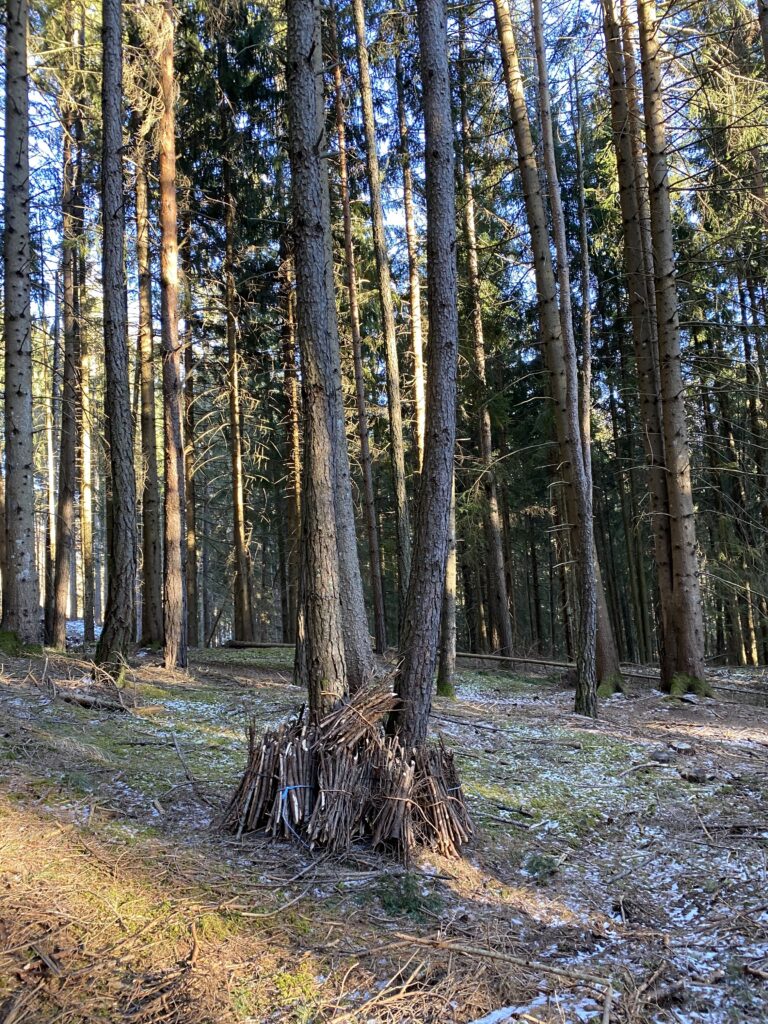
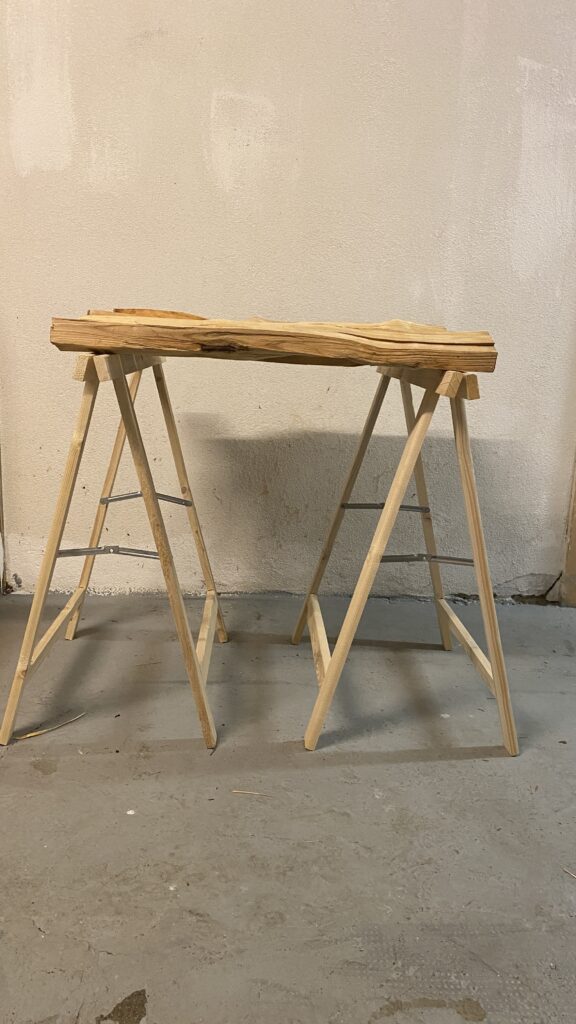
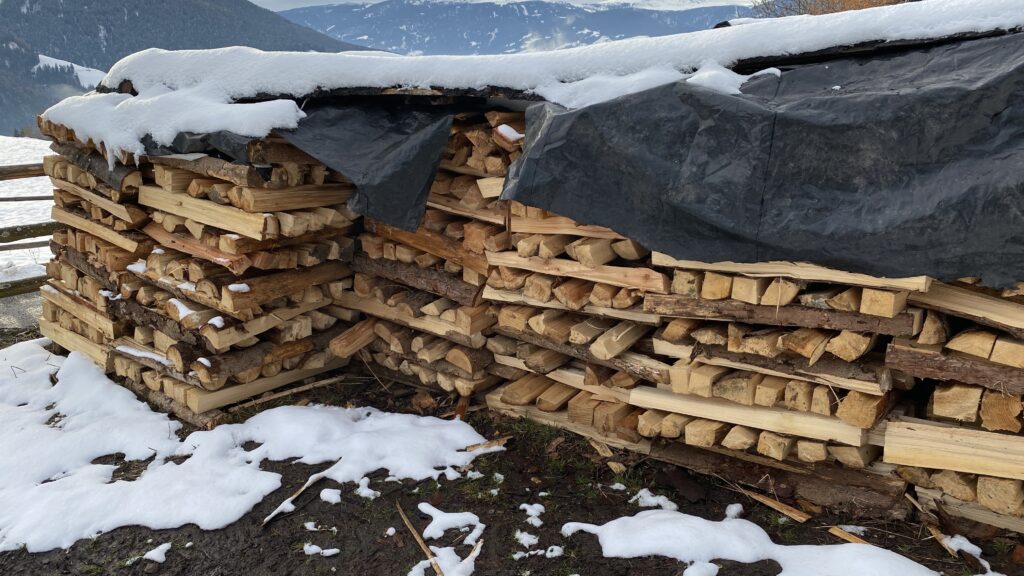
The aim was to give a new, more sensual surface to the material, which is completely focused on the user, and to place it on a higher level. On which its qualities can be appreciated. These messages are best expressed by the table. Because of its height, it is very easy to sweep over it. It is a piece of furniture that invites you to experience its haptic quality.
The first step is to choose the perfect material. As personal as the theme is, the material had to have a connection with me. My maternal grandparents are farmers in Villnöß and own some meadows and parts of a forest. From this forest trees are cut down to make firewood. The processing is done by my uncle, who has also taken over the farm. Depending on the type of wood, he first cuts the tree trunk into pieces up to 80 cm long and splits them with a special machine. Then the individual pieces of wood are stacked in layers to dry.
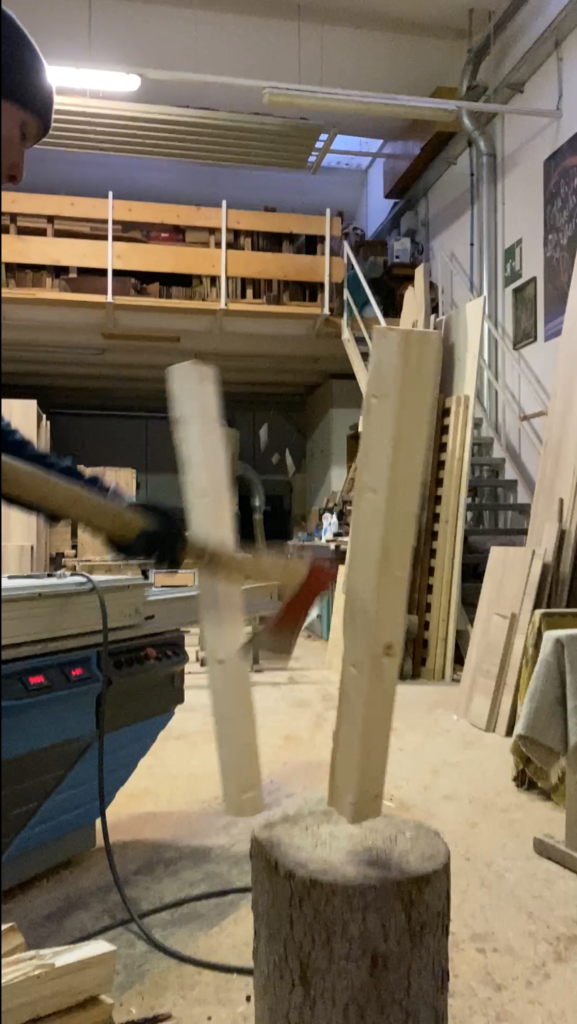
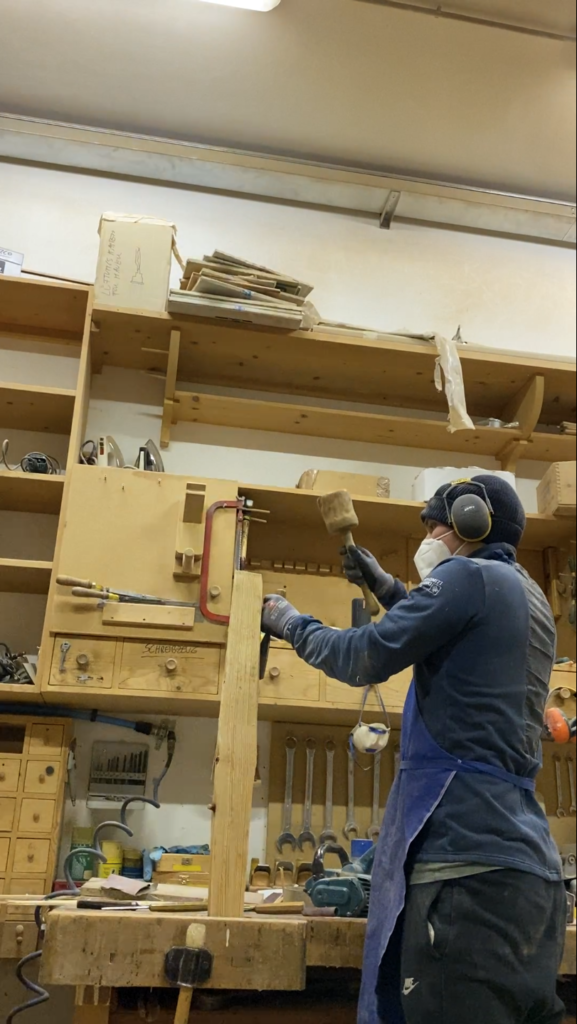
When selecting the individual pieces of wood, attention must be paid to several criteria. Are there any knots in the wood? How was the log split? What type of wood is it? Are there any discolorations?
After selection, they still need to be dried before processing. A few days on the stove in the living room was enough. The processing was done in the workshop of another uncle. First, the bark is removed and cut to size. An axe is used for this. To refine the still very rough wood a bit, it was first brushed on all sides and lightly sanded. In order not to lose the qualities of the wood, these tools were only used to a very limited extent. Then individual wood fibers were removed with the chisel. It is like carving, with one difference: instead of giving the wood a new shape, its form is retained and its qualities are brought out.
This procedure was repeated for each of the woods. After that, the end faces were removed with the circular saw on both sides.
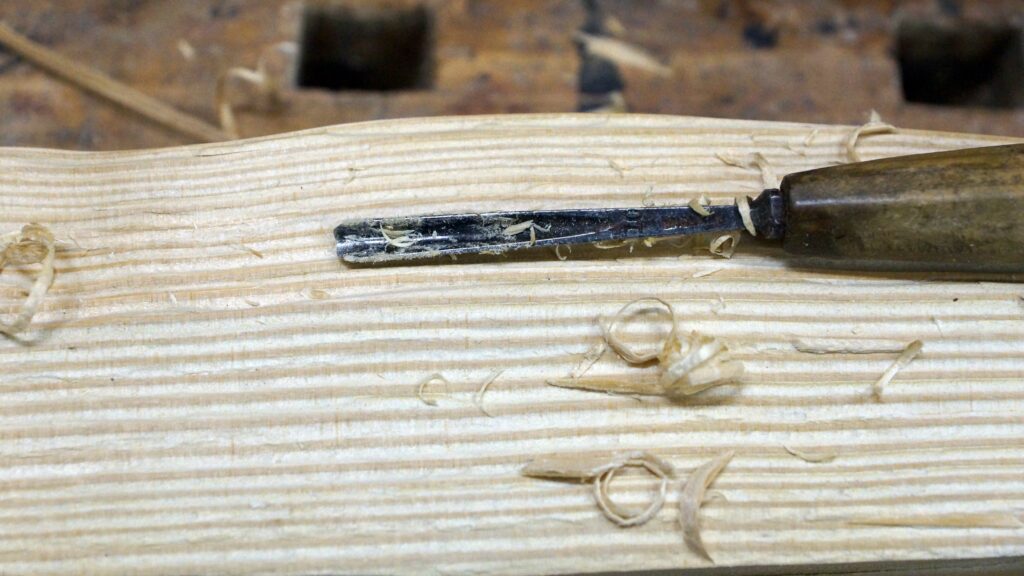
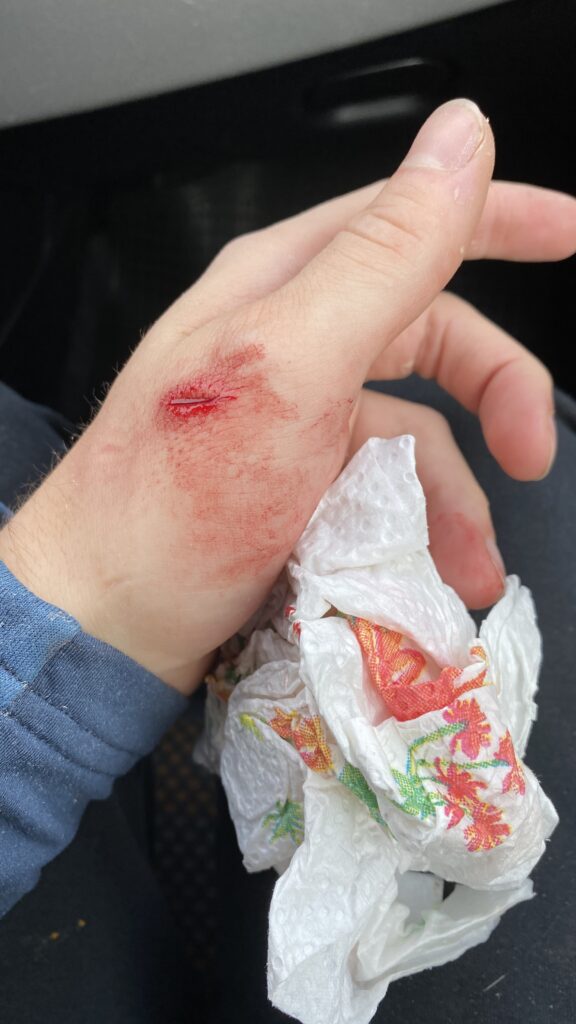
The table consists of two parts, the table top and the framework underneath. The framework is made of iron pipes with an outer diameter of 20 mm. Due to the ongoing pandemic, the workshop of the university could not be used, so the framework had to be made at a locksmith. Since the wood comes from Villnöß, also the scaffold should be manufactured in the same valley. The locksmith Steiner from St. Peter manufactured this part of the table, consisting of eight individual tubes, the two horizontally are perforated. At a distance of 5 cm to be as flexible as possible when attaching the timbers. Joining the two components is the final step. The timbers must now be arranged. A certain selection was made based on the type of wood, length and shape. Screws were used to fix the timbers from below.
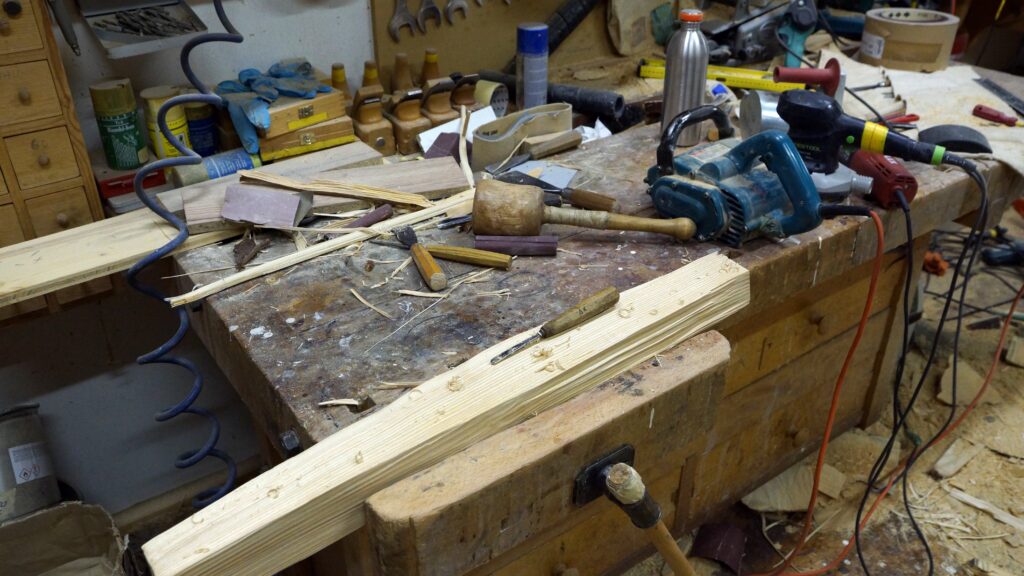